CO2 Laser Technology:
The CO2 laser beam is produced by exciting a mixture of gas. Its wavelength is in the mid-infrared portion of the light spectrum, meaning that the beam is beyond the range of human eyesight. It has a large thermal effect relative to other laser types and the focused spot is larger than focused spots of other lasers with smaller wavelengths. For instance, it is very common for flatbed CO2 lasers to have a .006″ spot size using what is called a 2 inch lens. For more on lenses, please click on “laser focus” just to the left on this page.
Materials commonly marked, cut or engraved using a CO2 laser include: wood, cardboard, silicone, metals, mylar, paper, cast acrylic, extruded acrylic, Delrin or acetyl, styrene, polyethylene, foam (non-PVC), glass, marble, granite, leather, fabrics, EPDM, Neoprene and rubber stamps.
Primarily, the CO2 laser wavelength is 10,600 nanometers. There are slight wavelength variations that can be found for very specific applications for beam absorption reasons, but 10,600 nanometers is typically sold for most applications requiring a CO2 laser.
In the industrial world, defined here as laser power 10 watts or higher, there are sealed laser tubes from 10 watts and up to 400 watts and then there are continuous flow tubes for laser power greater than 400 watts and well into the multi-kilowatt range. These lasers are primarily used for metal cutting, though you will see CO2 laser energy as low as 150 watts for cutting thin metals.
Lower CO2 wattage will have an effect on metal similar to the light from a flashlight bouncing off of a mirror. Higher power is needed to overcome the reflective surfaces for cutting metals. Metals can be marked using lower powered CO2 lasers, but it requires a secondary process using Cermark or Thermark.
Sealed CO2 lasers are difficult to build on a reliable basis and is the reason why there are so few manufacturers offering them. The sealed laser tube contains a proprietary gas mixture and only about 5% of the gas is actually carbon dioxide. This is what creates the actual laser beam when the gas is excited. Approximately 90% of the gas is helium and is used to help keep the gas mixture cool for stability. Helium is very difficult to contain as the gas molecules can escape through the walls of the sealed tube.
In addition, the high peak energies generated in the power supply can damage the electronics and cause the need for repair. Commonly, this is referred to as a laser tube recharge, though the gas in the tube is still OK. Another issue is trying to seal the gas mixture within the laser tube and compensate for thermal expansion of the metals and elastomers needed for the internal feedthroughs in and out of the tube.
Exciting the gas mixture can be done using high DC voltage or with RF energy. More commonly known as glass tubes or metal tubes respectively. Until recently, glass or metal were the only methods for creating CO2 energy in a sealed laser tube. A recent breakthrough using a ceramic core is now a third option.
Glass Tubes Or Metal Tubes Or Ceramic Tubes?
Glass tubes:
- Less expensive than metal or ceramic tubes and are Ok for “cutting” since they want to be “ON” all the time. Glass tubes are typically found in Chinese made laser systems
- Water cooled adding to the maintenance and electricity draw. Expect higher electricity bills and much more maintenance for the chiller
- High DC voltage – Be very careful operating and replacing the tube!
- Very slow pulsing when engraving and the laser works very hard causing the internally mounted metal electrodes to deteriorate quickly
- Low life time. Cutting – 1000-2000 hours. Engraving – approx. 300 hours
Metal Tubes:
- Continuous, fast pulsing
- Air Cooled and water cooled available. Air cooling very common for laser power under 100 watts
- RF (radio frequency) used to create the laser beam – safer then high DC voltage
- Cutting and engraving work well without effect on laser life
- Metal tube construction with welds and feed-throughs for internally mounted electrodes
- Lifetime is 5 to 10 years
Ceramic Tubes (CeramiCore)
- Continuous, fast pulsing
- Air Cooled and water cooled available. Air cooling very common for 120 watts and under
- RF (radio frequency) used to create the laser beam – safer then high DC voltage
- Cutting and engraving work well without effect on laser life
- Ceramic tube construction fused, not welded. Welds can outgas and possibly contaminate the gas mixture
- No seals or feed-throughs as electrodes are externally mounted. No chance for gas to escape or O-rings to deteriorate
- Research show up to 30% longer life time compared to metal tubes
- Up to 30% less energy consumption compared to glass or metal tubes due largely in part to the energy efficient RF supply
- Best beam quality for sharper results and least scorching when cutting
- Faster switching speeds (rise and fall time) – results in sharper engraving results and cutting thicker material
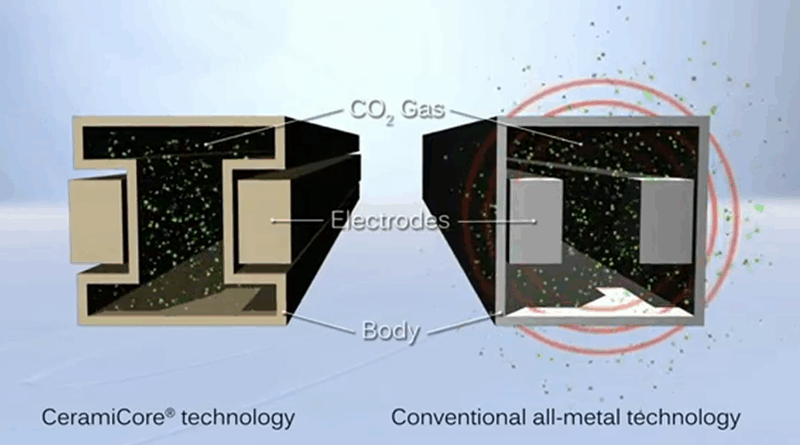